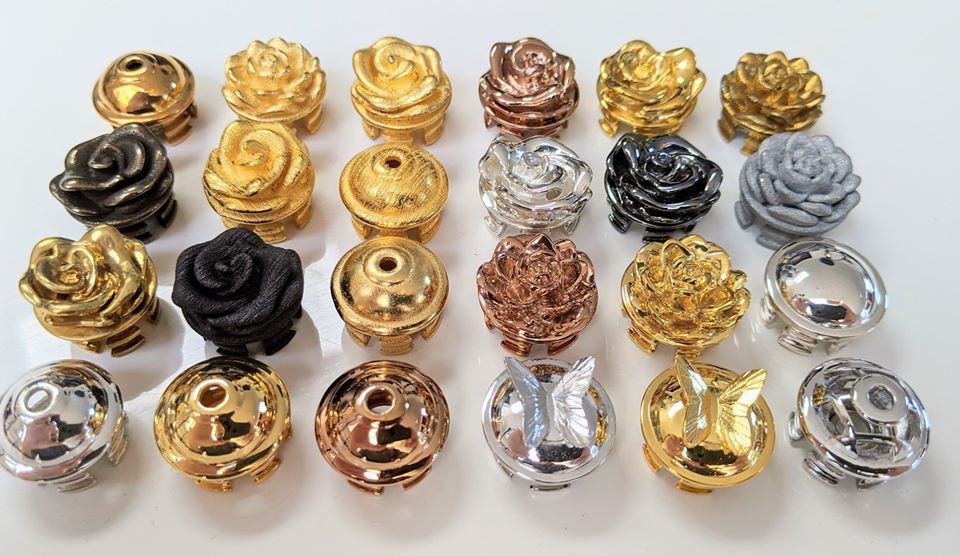
Interview with Peter Robertson
Flutist and product designer (UK)
öfg: First of all, thank you for taking the time to sit down and answer some questions. You’re a professional classical musician who plays in various prestigious orchestras, when and why did your interest in technology and design start?
Peter Robertson: I’ve always been interested in technology, and when choosing to go to university I was torn between studying physics or music – and eventually chose to study music at Oxford University. For the last 16 years or so I’ve split my time between predominantly amateur music-making and running tech and media companies in central London. Through that company, I’ve had the opportunity to design and build many interesting products and work on some amazing projects largely for other people.
More recently, after visiting Dr Robert Bigio for tutelage in flute head-joint making, I decided to try and combine my interests and apply some of what I do to flute making and flute gadgets. I have a special interest in magnets and in creating well-thought-through, reusable/multi-purpose products whether they are the software of physical – so I’m trying to apply those to my flute gadgets also. From my friendship with Dr Bigio I’ve come to realise that very little is truly novel, players and inventors of the past have attempted all manner of interesting innovations (some good and some hilariously silly) for the flute – but it is rewarding when I see players using my products.

öfg: Your most popular product are the so-called swap-stoppers. For someone who has never heard of them before, can you explain what they are and how they work?
PR: In each flute headhunt you will find some kind of “stopper” inside the tube at the crown end, just past the embouchure. Often this is made of cork and will have a silver, brass or steel disc on it.
Primarily, these are simply there to block that end of the tube, but also its position is important as it affects the intonation of the instrument. Each flute manufacturer will have their own preferred position determined by the scale of the instrument, the head-joint taper, and preference. This is often indicated, though sometimes not accurately, by the mark on your cleaning rod.
Stoppers should, in theory, have little effect on the sound quality or playing “feel” of the instrument – they are simply intended to block the end of the pipe! However, at one point in 2016 I changed the stopper in one of my flutes from the old cork to a small brass disk I made, partly because my cork was leaking and I had no replacement, and partly because I was helping a friend with wrist issues to lighten their instrument by reducing weight in the stopper, crown, and elsewhere.
The change in “feel” of the flute was tremendous. I immediately spoke with various flute player and maker friends, some of whom were adamant that changing the stopper affected the flute’s sound and others who strongly rejected the idea. Of those who thought it made a difference, there were various preferences as to weight and material. Once I’d noticed that players had different preferences for stopper weight and material, I decided to create a new kind of stopper that allowed the player to quickly change its material and weight easily (ideally during a performance even).
For my stoppers, there is a “back” piece that fits in place of your existing stopper, and there are swappable “faces,” in various materials, that you can quickly attach and detach along with attachments to the back to adjust the overall weight. This allows the player to “dial-in” their preferences to match different head-joints, musical preferences and even acoustics – and reuse the “faces” between different instruments.
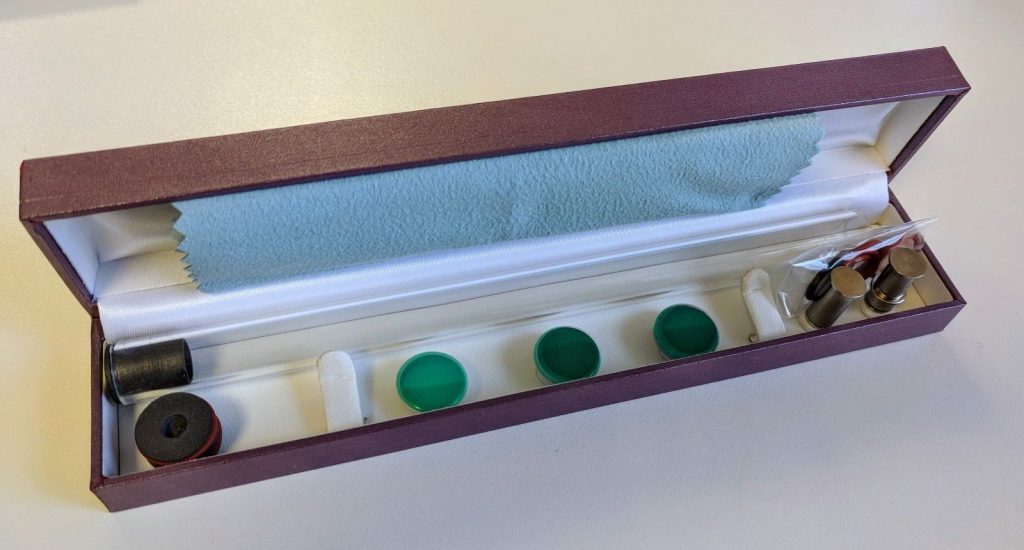
öfg: Besides a change in „feel“, why should someone replace their original cork with one of your stoppers? What is their benefit?
PR: Corks often need changing as they can dry and shrink over time creating leaks in your head-joint. So it is wise to get your cork checked or replaced whenever you get your instrument serviced. The advantage of some more modern, non-cork stoppers are that they avoid this drying/shrinkage issues as they commonly seal with o-rings that are resilient and long-lasting and cheap to replace. These kinds of stoppers are also easy to position and remove for cleaning.
öfg: In your Swap-Stopper Kit one can find stoppers with different face-materials. Can you give some insights in how the different materials affect the flute sound?
PR: Changing the “face,” for many players, seems to be similar to changing the blowing edge/riser material on the embouchure: it affects resistance, response, and timbre. Each material and finish (matt or polished, flat or curved) can feel quite distinct to play and perhaps suit different playing styles, acoustics and musical style.
I’ve experimented with over 50 different materials and shapes, from platinum to sapphire; with manufacturing techniques including forging, casting, sintering, and 3d printing and with many variations of size, shape, and finish. There is a significant difference in the perceived affect of materials and weights close-to (to the player) and for the listener. I’ve decided on a starter kit that includes silver, titanium, and zirconium faces as they are attractive to play, and cost-effective, although production of the parts with a mirror finish in titanium and zirconium is a challenge! These three materials, in the weights, selected, produce a great range of feel to experiment with, without the onerous expense associated with golds and platinum.
Small things make a difference, and each flute and player is unique. The important thing for me is that the kit provides a wide range of options so that the player can match the setup to their playing and their instrument. I sometimes change setup in a rehearsal: maybe I’m just not projecting or blending, or having a “bad playing day,” and changing to a different stopper face can give me the change I need to reset my playing which, for me, often involves swapping to a face that I feel gives my head-joint more or less resistance and therefore altering my control.
öfg: Would you say that these stoppers are suitable for all levels of flute playing and all types of flutes?
PR: I think all flutes can use new-style (non-cork) stoppers. In fact, I’d suggest that all manufacturers of student and intermediate instruments should probably swap to using them as these are often instruments that their players cannot arrange (or cannot afford) to get serviced regularly. I’m working with one manufacturer to try and create a new (non-swappable) stopper to do just this. The swap-stopper, though, is aimed at advanced amateurs and professionals. It is not suitable for kids due to the magnets used. You should really have a well-setup instrument, with well-fitting head-joint, free of leaks, before experimenting with any kind of flute gadget. I personally think that the good-fitting of a head-joint can have far more effect on your playing and the feel of a flute than many of the add-on gadgets that are available.
Customising is best done when you are comfortable with your own technique, and able to critically judge the effects of changes in resistance and attack. Assessing any flute gadget should be done across a range of days, in varying circumstances and in different acoustics, and ideally by getting feedback from colleagues. What sounds powerful in your living room may not carry for you across a large symphony orchestra. For someone else, it might.
öfg: On your website flutegadgets.co.uk you also offer extraordinary and colourful crowns, what inspired you for these special designs and what is your personal favourite?
PR: I had an idea in my mind for a rose-design crown that I wanted to make for myself. Prototyping included creating some lightweight plastic versions so that I could experiment with shapes and fitment. These looked attractive so I gave a few away as gifts, and then began selling some and soon it turned into a bigger thing! They are primarily aimed at kids and I love coming across pictures on Facebook of teachers with their students holding their flutes up to create a row of colourful roses 😉
A teacher in the US asked me to create sparkly ones for her students, and after a bit of experimentation I made purple, pink and black sparkly versions. And these have become my personal favourites amongst these colourful ones. My overall favourite is a close tie between a solid gold one I made for a fantastic US player, it felt amazing to hold and I was sorely tempted to keep it for myself, and a simple silver butterfly.

öfg: What other products are planned for the future? What is your vision for the next 10 years when it comes to flute gadgets?
PR: I’ve been quiet busy making some custom faces in novel materials (e.g. wood and sapphire) and bespoke crowns to fulfil commissions. There are a couple of face materials that are proving popular which I’d like to add to the standard kit. I’ve some other silly ideas in development but they may well be infeasible!
I think in general, there is much innovation that can be made in the areas of flute keywork and pads. I hate flute pads, those little annoying flimsy temperamental (and quite expensive) things that can wreck a performance! I do wish someone would come up with a resilient and well-sealing alternative. I also suspect we will see more gadgets including electronics, and additive techniques for forming mechanisms and eventually tubes.
öfg: Besides performing in orchestras and developing products you are also quite active on social media platforms like instagram and twitter. Is it nowadays important for small businesses and for musicians in general to be present there?
PR: It seems essential career-wise nowadays to have a presence on social media. It is both liberating, being able to self-publicise, and also daunting. Those I see succeeding certainly have a strategy: they post regularly, they time it well and adjust their creations for their audience. It takes significant effort and time to do it well and I certainly do not do it well. 🙂
Music for me is a fantastic way to reach out into the world, to meet people, to expand my horizons. I’m somewhat an introvert and so social media helps me to do that. I’ve met some amazing flute players and makers, had passionate discussions, and travelled the world thanks to the contacts I’ve made via platforms such as Facebook and Instagram.
öfg: Last question, in 2006 you co-founded Upbeat Productions, a digital production agency, specialising in software development and video production services. How do you manage working on two businesses and performing on stages regularly? Is it in your opinion vital to develop a second mainstay as a musician?
PR: I always wanted to have a varied career, so early on I tried to do as many different things as time allowed. Perhaps my music-making has suffered from my business life – but then I’d not have been involved in creating a cartoon series, or creating the world’s first classical music streaming service or work on Harry Potter. Perhaps my business-life has suffered from the “distractions” of music – but then I’d miss out on working with amazing colleagues, playing big solos in a huge symphony orchestra, or standing in front of one playing a concerto or playing a piece written for me. My business-work sadly means that I can I only have time to perform 15-30 concerts per year, so I have to choose carefully what I can take on. Regular, effective practise time is the most difficult thing to achieve. And you never truly escape the worries and pressures of business-life.
Multiple-careers are not really a new thing – at least not for musicians, who are used to combining performing, teaching, composing, arranging, academia, marketing, administrative jobs etc, and a wider-variety of other professions and enterprises. I think, especially through social media, we get more insight into the choices that musicians have to make to balance their passion with realistic economics, and into their other interests and abilities.
I also feel that there are increasing opportunities and acceptance of multiple-careers (both simultaneous and sequential), and being able to work remotely and using new digital tools increases the range of opportunities which can empower musicians. It is certainly vital to understand the realities of a career in the arts, and cultivating other skills and interests is probably a benefit. Sadly, very few can earn a living solely from playing and I like to think that through our other careers and businesses we can help support creative organisations, composers, and makers, and ensure that both amateur and professional music-making can thrive.
Peter is a London-based flute player who performs regularly as principal of the Ealing Symphony Orchestra and Oxford Chamber Orchestra. He plays a special gold Haynes flute (#7) and wood flutes by Chris Abell with a Robert Bigio Mopane wood head-joint. Peter has wide ranging interests as a technologist and product designer, and as well as playing flutes to a professional standard is very interested in flute building, flute gadgets and accessories. He is currently experimenting with new flute design.
Instagram: @flutealot
Webseite: https://www.peterrobertson.name
Products: https://flutegadgets.co.uk/
The interview was led by Mirjam Braun for the ÖFG.
A selection of crowns (metal and plastic), and a stopper kit for testing is available from Maria Kosa (ÖFG board), and can be viewed, tested and purchased by appointment.
Contact: office@oefg.net or 0650 5160 073.
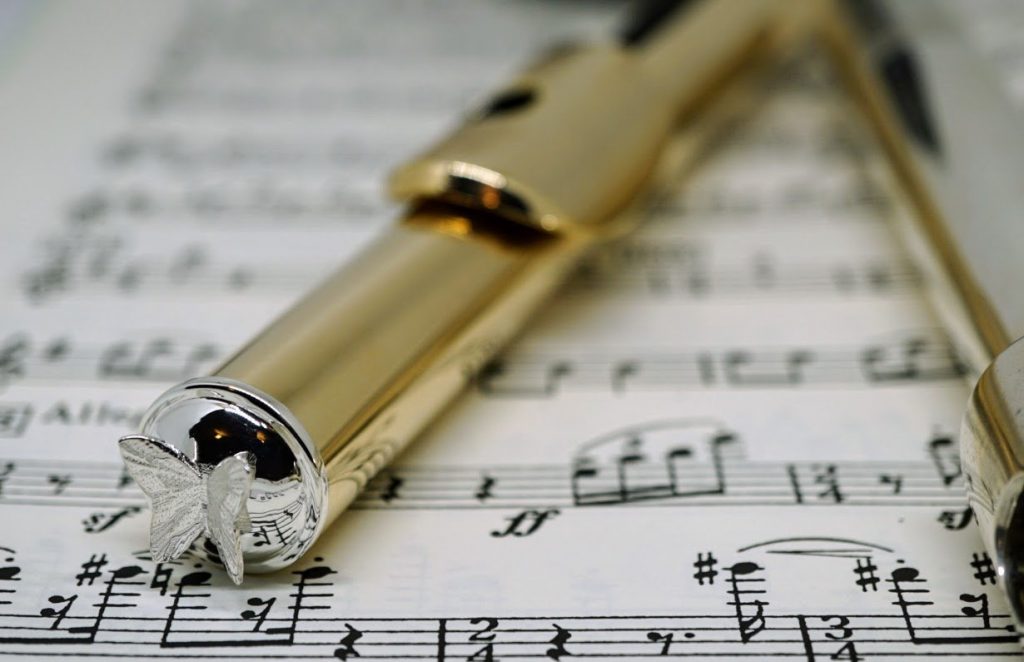

